AI & Automation: Real Tips From Real CEOs
Rising wages and a shortage of skilled workers are driving CEOs to push artificial intelligence and robotics deeper into their operations. Here's what some of them are learning along the way.
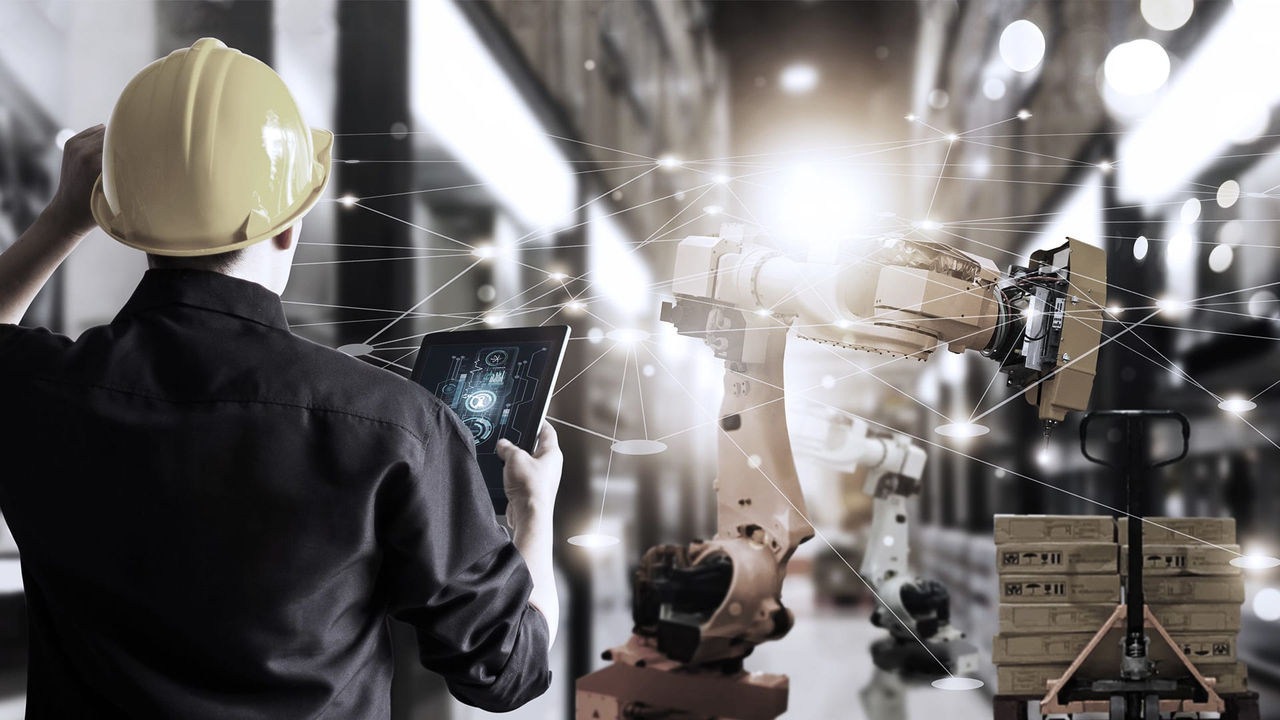
Rising wages and a shortage of skilled workers are driving CEOs to push artificial intelligence and robotics deeper into their operations. Here's what some of them are learning along the way.